Building Tomorrow - 3D Printing's Green Revolution in Construction

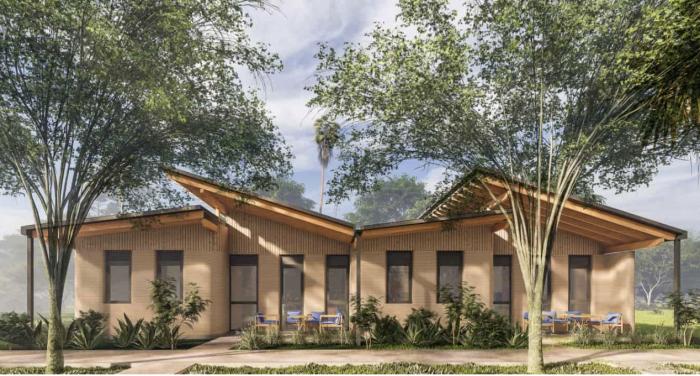
Construction technology is advancing after years of lagging digitalization, and 3D printing is becoming the spotlight for revolutionizing construction methodology. Companies like Peri Group, and ICON are exploring the potential of 3D printing to reshape construction. Their collective vision? To minimize environmental impact and make construction faster, more efficient, sustainable, and productive.
ICON, for instance, wowed everyone by constructing a single-family home in Austin within eight days, challenging the conventions of conventional construction schedules, which, according to the 2021 report from the U.S. Census Bureau, the average time to build a single-family home is between 7 and 12 months.
ICON's 3D printing methodology involves making materials such as Lavacrete, a rock-solid mix of red pulverized lava rock, cement, and water. Then, their trusty 'Vulcan' 3D printer pumps this mixture onto the ground or a slab in record time. With the help of BuildOS software, digital designs spring to life as real homes, cutting waste by a massive 30%! That's not just because it avoids mistakes but because it uses only what's necessary. Any leftovers are easily recycled for future projects.
A significant challenge has been the costs and rules holding this tech back. According to the article "Additive Manufacturing in the Construction Industry: The Comparative Competitiveness of 3D Concrete Printing" by MDPI Applied Science, it is essential to take into consideration the costs of printed construction the skilled labor, a forklift rental, and a two-axle truck capable of transporting the 3D printing components around the site during the printing process, which consumes a large budget. For example, a Kustom StroyBot 6.2 3D printer with a maximum build size of 10 x 20 x 6 meters (LxWxH) starts at $300,000 and can cost up to $950,000, depending on the model and build envelope required. However, speedier construction methods are needed with a housing crisis leaving a shortage of 2 million homes annually in the U.S. This movement isn't just about making it faster; it's about creating more intelligence, being greener, and setting the stage for a sustainable future.
Also, this new technology is facing a big challenge, mainly for commercial and public building construction. The reason is related to the building code rules; everything must be tested in many ways before approval, such as fire, water, and structural testing. It’s a long and expensive process, where the tests are tied to specific formulas and geometries that cannot be changed.
3D printing is evolving to be the next significant advancement in construction. As the costs drop and technology gets even better, its potential to change how we build homes strengthens. The difference between a conventional construction cost and a 3D Printed house cost is significant. According to a recent article in the World Economic Forum, 3D printed houses can cost up to 45% less than houses built with traditional methods, while the cost to build an average-sized 3-bedroom house with conventional building methods is from $250,000 to $320,000, that same 3-bedroom house would presumably cost between $140,000 to $180,000 to build with 3D printing technology.
Moreover, the environmental impact of this technological shift must be balanced. According to the United States Environment Protection Agency, the waste report for construction and demolitions shows in the Advancing Sustainable Materials Management 2018 fact sheet that the construction sector generates a staggering 600 million tons of waste in the U.S. annually, with only a fraction recycled, leaving the rest to pollute landfills. Embracing 3D printing in construction could reduce this to 30% to 40% less waste and foster a circular approach by recycling materials like cement and plastic.
Furthermore, in collaboration with NASA, ICON spearheads Project Olympics to construct lunar homes for scientists and, eventually, ordinary citizens on the moon. Given the exorbitant cost of transporting materials to the moon, the proposed approach revolves around dispatching a 3D printer to the moon, harnessing lunar concrete extracted from rock chips, mineral fragments, and dust on the moon's surface to erect these structures. This ambitious initiative is to develop homes that can self-sustain on the moon. This leads to the vision extending to easier development of self-sustainable homes on Earth, promoting reduced environmental material usage and paving the way for a more eco-conscious future.
This technology will revolutionize the industry and enhance efficiency, rapid prototyping, design flexibility, waste reduction, material durability, and affordable housing, shaping a greener, more sustainable future for construction worldwide.
Tecla house (Copyright © Mario Cucinella Architects and WASP, 2021). Photos by Iago Corazza.
PHOTO CREDIT: CASEY DUNN
PHOTO CREDIT: House Zero, CASEY DUNN
ICON'S Vulcan Home-Sizd 3D Printer
To read more about 3D printing technology:
https://www.mdpi.com/2075-5309/12/10/1703
https://www.aniwaa.com/buyers-guide/3d-printers/house-3d-printer-construction/
https://www.xometry.com/resources/3d-printing/best-3d-printers-for-construction/
United States Environmental Protection. (2018). Advancing Sustainable Materials Management: 2018 Fact Sheet.
https://3dprintingindustry.com/news/nasa-confident-of-3d-printing-houses-on-the-moon-by-2040-225318/
https://www.peri.com/en/business-segments/3d-construction-printing.html
https://www.3dwasp.com/en/3d-printed-house-tecla/
https://www.iconbuild.com/projects
Title Image: Edge Buildings, Mulve Gardens by 14 Trees
- Filed Under: Modular Homes
- ( 2606 ) views

I am an Architect and Urban Planner graduated in Brazil and working with architecture since 2013. Nowadays I am living in Boston area. I have Zero Energy Building course completed in Harvard Extension School and this year could get my LEED GA credential. My interest in Sustainability and Green Buildings is growing up every day and becoming my focus, therefore my aspiration is to gain more experience and help people with my expertise.
- ( 0 ) Ratings
- ( 5 ) Discussions
- ( 5 ) Group Posts
Reply/Leave a Comment (You must be logged in to leave a comment)
You are bound to fall in love with our manufactured homes in Holiday West which are located in Sumpter Township. It houses the Crosswinds Marsh Preserve and the Wayne County Parks which offer plenty of facilities. Nature enthusiasts will love it here where they stand to enjoy activities like hiking, horseback riding, cross country skiing, canoeing and fishing which are just a short drive away from Holiday West community. To experience an estate with a country feel that is surrounded with numerous amenities, inquire about our manufactured homes in Holiday West today.
Connect with us!
Subscribe to our monthly newsletter:
Not a Member Yet? Register and Join the Community | Log in